


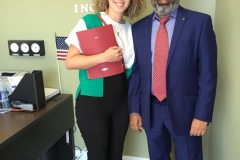
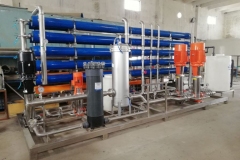




frequency and voltage of its power supply. The VFD also has the capacity to control ramp-up and ramp-down of the A variable frequency drive (VFD) is a type of motor controller that drives an electric motor by varying the motor during start or stop, respectively.
Even though the drive controls the frequency and voltage of power supplied to the motor, we often refer to this as speed control, since the result is an adjustment of motor speed.
There are many reasons why we may want to adjust this motor speed.
For example, to
In addition, today’s drives integrate networking and diagnostic capabilities to better control performance and increase productivity. So, energy savings, intelligent motor control and reduction of peak-current drawn are three great reasons to choose a VFD as the controller in every motor-driven system.
The most common uses of a VFD are for control of fans, pumps and compressors, and these applications account for 75% of all drives operating globally.
Soft starters and across-the-line contactors are other, less sophisticated types of motor controllers. A soft starter is a solid-state device and provides a gentle ramp-up to full speed during startup of an electric motor.
An across-the-line contactor is a type of motor controller that applies the full line voltage to an electric motor.
The difference between drives from Danfoss and other suppliers is that Danfoss is global market leader in VFDs, specializing in drives only. You receive a high-quality drive which you have customized to your exact requirements. And every single drive is thoroughly tested before leaving the factory. Our experts are focused on every possible detail of drive optimization, and are always abreast of the newest technological developments. Often, we invent the newest developments. Danfoss Drives has a broad offering of VLT® and VACON® drives, and you get much more than the drive itself. You also have access to our application know-how and a range of maintenance services to keep your systems running optimally throughout the drive lifecycle.
We offer you the best possible components and full flexibility so you can fine tune system performance to suit your application exactly. An important aspect of this flexibility is the ability to use your drives with all typical motor technologies, since VLT® and VACON® drives are designed for full compatibility. This enables significant savings in spare part inventories and in retrofit situations.
Motor Independence – One VLT® for all motors
A variable frequency drive can use VFD control to vary the power supplied to match the energy requirement of the driven equipment, and this is how it saves energy or optimizes energy consumption.
The drive can dramatically reduce energy consumption when compared to direct-on-line (DOL) operation, where the motor runs at full speed regardless of the demand. Using a drive, power or fuel savings of 40% are common. The roll-on effect means that use of drives also the reduces NOx emissions and CO2 footprint of the systems in which it’s installed.
None. All these names refer to the same kind of devices, also known AC variable speed drives, AC variable frequency drives, VFD inverters or variable voltage variable frequency drives.
There are many diverse types of drives available since they are widely used in industry. Both single-phase VFDs and three-phase VFDs have evolved to suit a wide variety of applications. The differences in drive types include the methods used for frequency and voltage control; and harmonic mitigation technology.
The three major variable frequency designs used in drives are pulse-width modulation (PWM), current source inverter and voltage source inverter. The PWM technique is the most common. The PWM technique requires switching the AC drive’s inverter power devices – transistors or insulated-gate bipolar transistors (IGBTs) – on and off many times, to generate the proper root-mean-square (RMS) voltage levels. Controlling and varying the width of the pulses is how PWM varies the output frequency and voltage to achieve VFD control.